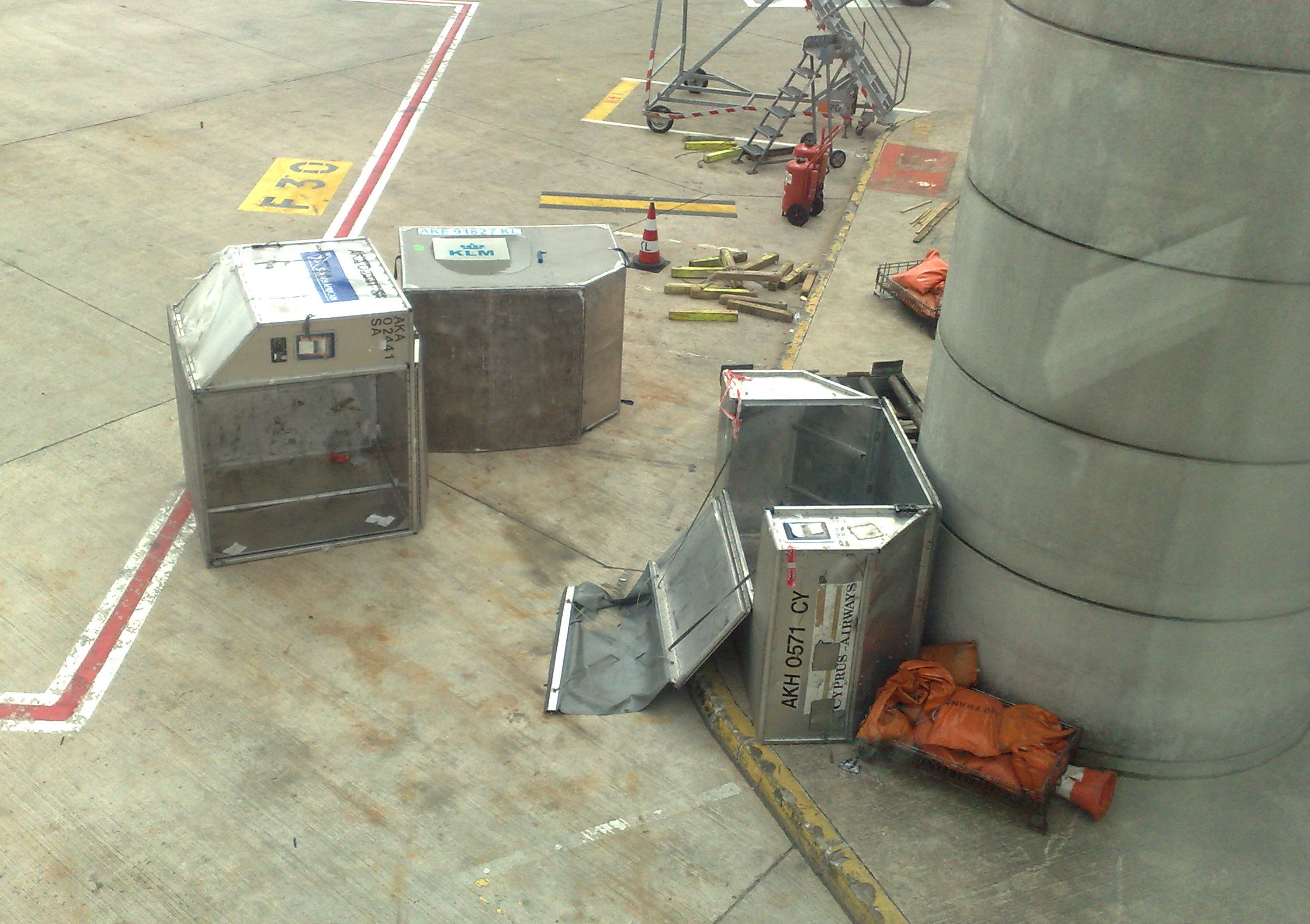
According to IATA’s ULD Safety campaign, ULD repairs cost the industry US $ 330 million annually, of which 80% could be avoided if they are handled correctly. Still considered the number one cause of aircraft damage among all ground operations equipment, most issues stem from mishandling, lack of proper storage and most notably the lack of awareness that a ULD is an aircraft part.
ULD operations are under-recognized across the industry, this includes among some of the regulators. A major contributing factor is the widespread lack of industry understanding that ULDs are aircraft parts. Th is is partly due to the International Civil Aviation Organization (ICAO) and Civil Aviation Authority (CAA) regulations use of general terms such as ‘aircraft part’, ‘component’ or ‘appliance’ by which the ULD has been both ‘covered’ and ‘hidden’.
Ground Handling Operations
Another challenge in ULD safety is the complex ground handling operations set up in aviation. ULD are the only aircraft parts to leave control of the airline and return back on board after passing through many ‘unregulated’ hands (not directly governed by airworthiness regulations). Ground handlers, cargo terminals and freight forwarders all play a very important role in the ULD operational chain, but very little importance is placed on ensuring that stakeholders are aware that ULDs are aircraft parts that when placed in the aircraft, must deliver on both flight safety and regulatory compliance. Th is has left the ULD handling process open to high levels of vulnerability in the entire chain.
To keep up with the times, aircraft have not only grown but advanced profoundly over the years, take a typical 7879, A350XWB or 777-300 which carries more than double the cargo and baggage of earlier models from the 1970s. Yet, it is not uncommon to find 1970s technology ramp practises for loading and unloading still used today, including the same amount of manpower.
But ramp teams aren’t the only vulnerable link, as they often receive unsafe, non-compliant or non-airworthy loads from upstream at the cargo terminal. A major airline in Hong Kong indicated that more than 80% of the ULDs exported from Hong Kong are built up by freight forwarders. If a major cargo terminal operator handles more than 100 airline customs, it’s believed that a clear majority of the airline’s ground operations are 100% outsourced in stations away from the airline hubs.
In-House vs Outsourcing
In the 50 years since the wide-body aircraft first made an appearance, the entire field of ground handling and air cargo operations has undergone a seismic shift. Not only has there been enormous growth in volume but simultaneously airlines have aggressively pursued a move away from being all-purpose operators to outsourcing anything not defined as a “core activity”. This has led to an almost total delegation of ground handling and air cargo operations to third-party service providers. Most ULD operations today are outsourced and performed by non-airline parties.
Th e industry evolution of outsourcing was not reflected in the ULD regulatory framework, in which only airlines were fully covered under the safety and airworthiness requirements for ULD operations. Non-airline parties such as ground handling agents, cargo terminal operators and freight forwarders were not subject to ULD safety and airworthiness regulations. As such, these critical ULD supply chain partners had no directly regulatory liability in the case of non-standard practices or subpar performance.
An aspect that seems to be forgotten more often than not, is that the most important purpose of a ULD is to secure loads during a flight. Staff in the warehouse responsible for ULD buildup and staff on the ramp in charge of aircraft loading and restraining ULDs have been found to have a general lack of safety awareness and understanding of the catastrophic consequences that incorrect ULD handling and restraint can cause.
Answerability
Despite challenges that may arise during the ground handling operations, it is interesting to note that airlines are still ultimately responsible for the security of the cargo and safety of flight. Irrespective of certain roles being outsourced or not.
The Fine Air 101 (1997) and National Air Cargo 102 (2013) flight crashes are among the most significant and talked about incidents when referencing accidents where an issue with the cargo is believed to be the culprit. Th e first prompting the Federal Aviation Administration (FAA) to publish the advisory circular providing operators with recommended procedures for managing cargo operations, the AC 120- 85. Th is had a momentous impact on airlines, as random checks carried out by ramp inspectors on cargo coming into the United States revealed many failures, especially relating to the improper use of ULDs, non-serviceable nets, poor loads, overweight, or oversize cargo (to name a few).
Driving Change
Along with the regulators, associations such as IATA and ULD Care have made a stand and are still pushing for change.
IATA is working with the industry to address the issue of supply chain accountability. Leading the charge is the IATA ULD Board (ULDB). Its members are engaged in consultation with all segments of the air transport industry, including airlines, aircraft and ULD manufacturers, regulators, ground service providers and freight forwarders; as well as professional institutions such as International Standards Organization (ISO) and the Society of Automotive Engineers (SAE International), to develop the IATA ULD Regulations (ULDR). Th ese are a comprehensive single set of guidelines that are in full compliance with regulatory and airline requirements for all parties involved in ULD handling and operations.
However, all the guidelines and regulations in the world are meaningless without those responsible for the implementation and monitoring being qualified and trained. In the past, formal ULD training was superseded by tribal knowledge and ULD training requirements were just a “ticking the box exercise.”
Luckily this is changing, ULDR has clearly outlined the ULD training requirements, directly corresponding with the functions, tasks and responsibilities of the staff , regardless of which organisation they are from (for both airlines or nonairlines companies). Like a competent driver with a driver’s license, only staff who understand the industry requirements will be allowed to handle a ULD. Th is will ensure compliance with all safety and airworthiness requirements.
IATA ULD Safety Campaign
In a further commitment to reinforce ULD safety, IATA launched an industrywide safety campaign in 2016, to raise the ULD safety awareness and reduce the number of ground handling incidents involving ULDs.
The campaign targets all stakeholders in the ULD value chain from ground operations staff through to regulators. IATA’s objective is to save the cargo industry over $400 million annually through promoting correct ULD handling; also minimising flight safety risk and the number of incidents of aircraft and container damage from mishandling.
The ULD Safety Campaign artwork, communicating 5 key messages, was downloaded by over 700 stakeholders. Eighteen companies have confirmed they are championing the campaign. In one case the ULD damage rate dropped “from a whopping 30-35% to an acceptable 10-15%” and ULD related findings in the various inspections carried out by safety regulators dropped down to zero and remained unchanged.
A Social Media campaign was also launched, aimed at sensitising the non-technical aviation community. A resounding success, the ULD Quiz on IATA’s Facebook page was the most engaged IATA post on the social media platform in August 2016.
Further Training
IATA also provides ULD Training programs that are aimed at increasing the level of operational competence and raise industry-wide safety through the implementation of industry standards and regulations. Th e training programs have been developed with the learner in mind to optimise the learning experience through best practice examples and case studies. Th ere are two classroom programs currently on offer: ULD Operations Training and ULD Trainthe- Trainer.
The first program has had over 230 participants from over 30 different countries over the last 5 years; while over 30 participants since its debut in October 2016 have taken part in the second.
ULD Care also pushes for change
Th e brainchild of ULD Care, SOSULD is one of the steps the organisation has taken to initiate an industry-wide mindset change. Speaking about the video, Bob Rogers, vice president of ULD Care said:” it was the result of a decision by ULD Care that we needed a professional way to reach industry stakeholders, and when it comes to ULD a picture is worth a 1000 words and moving pictures worth 1000 still picture. It was the first eff ort and turned out remarkably well, opening the door for conversations with stakeholders in the industry who were not aware of the ULD safety, operational and cost issues.”
SOS-ULD fully demonstrated the power of video, prompting ULD Care to consider alternatives like video training, using animation and investigating the possibility of suitable training in diff erent features, such as ULD storage, ULD inspection and ULD build-up.
ULD Explained
Th ere are many commercial guides on various aspects of the aircraft and airline industry but this is the first purely focused on ULDs. ULD explained is designed to do exactly what its title says, provide an easy to read explanation of the ins and outs of ULD activity, with guidance on why things need to be done a certain way and how to do it that way. At about 50,000 words and almost 150 captioned pictures to illustrate many points, it is the perfect “go to” for anyone wanting to know more about ULD. Plans are in place to off er translations in other languages as time goes by.