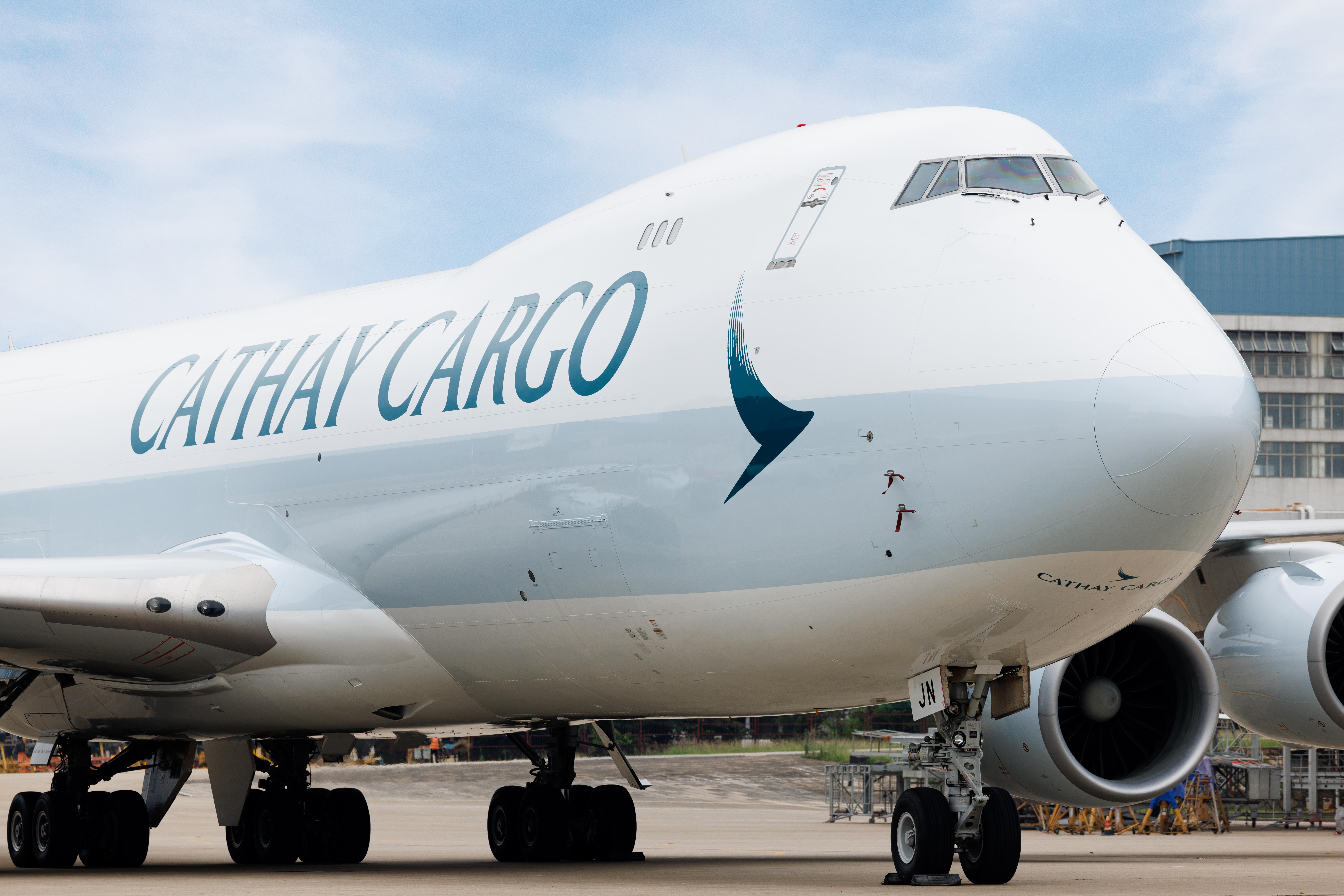
Safety is paramount in the transportation of dangerous goods and pharmaceuticals. Every shipment carries not just valuable cargo but also the potential for catastrophic consequences if mishandled. The stakes are immense–from lithium batteries that can ignite without warning to temperature-sensitive pharmaceuticals critical to public health.
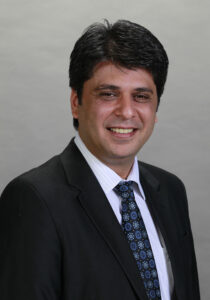
Recognising these challenges, industry leaders like Cathay Cargo have made safety excellence the cornerstone of their operations. By implementing rigorous risk assessment protocols, embracing continuous innovation, and prioritising comprehensive training programs, Cathay Cargo ensures that every shipment is handled with the utmost care—safeguarding both the cargo and the people who depend on it. In an exclusive interview, Ashish Kapur, Cathay Cargo’s Regional Head of Cargo, Southeast Asia, shares valuable insights into how the company upholds these high standards in the face of ever-evolving industry demands.
Payload Asia (PA): Given Cathay Cargo’s comprehensive risk assessment protocols, could you elaborate on how these processes have evolved to manage the complexities of shipping dangerous goods?
Ashish Kapur (AK): At Cathay, safety excellence is the cornerstone of our success. We are IOSA and CEIV Lithium Battery accredited. We implemented a Safety Management System (SMS) as a systematic, detailed, and proactive process for safety management. All cargo employees undergo comprehensive training and are certified to provide regulated handling at all stations, including collaborating closely with IATA, government regulators, cargo terminal operators and customers to ensure service and safety standards are above par.
With our unwavering focus on safety, we will continue to innovate and optimise our processes around the safe carriage of dangerous goods through the digitisation transformation journey. Notable initiatives include the implementation of electronic Dangerous Goods Declaration, NOTOC (Notification to Captain) and checklists.
PA: Cathay Cargo is at the forefront of employing innovative technologies for safety and efficiency. What are some recent technological advancements that have significantly enhanced your handling of dangerous goods?
AK: The Dangerous Goods Digitisation Project is currently in the BCD (Business Case Development) stage, which is a significant milestone in our commitment to enhancing our dangerous goods handling process. We aim to develop a common platform that seamlessly manages all the data, documents, and operations through digitisation. By doing so, we aim to optimise our end-to-end process and ensure efficiency and safety at all times.
PA: As Cathay Cargo prioritises rigorous training, what are some insights into these programmes that are continually updates and what skills are emphasised as regulations change?
AK: Our approach to DG handling involves a comprehensive review and refinement of our processes, incorporating firsthand experience and feedback from all levels of DG handling. This presents us with an opportunity to innovate our learning methods, ensuring that the latest information on DG handling is shared across all levels.
We recognise the importance of continuous learning and ensuring everyone receives the most up-to-date information. To achieve this, we adopted the Competency-based training assessment (CBTA) module following the functions stated in IATA’s Dangerous Goods Training Guidance. Group discussions for real-world case studies and interactive exercises are conducted in our DG classroom training. We are also moving beyond traditional classroom learning and exploring new DG CBT training modules that engage our people through educational games and virtual reality learning. We believe this will stimulate their interest and enhance their learning experience.
PA: With Cathay Cargo’s integration of cutting-edge technology for shipment tracking, how has this technology particularly improved your management of dangerous goods?
AK: We take pride in our end-to-end shipment tracking capabilities. From the moment a shipment is accepted, we can track and have full visibility of the shipment until it reaches its destination. Our customers, too, receive the same level of insight.
Cathay Cargo’s multi-dimensional track-and-trace service, known as Ultra Track, gives customers near-real-time information on the airport-to-airport leg of the shipment journey using low-energy Bluetooth data loggers. With this, we can monitor the shipment regularly and provide 24/7 proactive support and intervention on shipment irregularities. For example, we can check the shipment’s temperature status throughout the journey, ensuring the cargo’s integrity.
Cathay Cargo also implemented the Cargo IQ Master Operating Plan (MOP), which has been endorsed by IATA as a recommended industry practice. This includes various milestones that enable us to monitor the entire process of transporting air cargo from shipper to consignee.
PA: As Cathay Cargo navigates the complex landscape of international regulations, what are the most significant compliance challenges you face with dangerous goods, and what strategies have proven effective in addressing these?
AK: The carriage of mis-declared and un-declared dangerous goods poses significant threats to aviation safety. At Cathay Cargo, we take a proactive stance in cargo screening, having implemented the Cargo Agent Operation Program (CAOP) to assess cargo agent’s performance when handling DG shipments. Control measures have also been strengthened to prevent incidents involving dangerous goods.
PA: What are some insights into Cathay Cargo’s approach to incident management involving dangerous goods? What critical lessons have been learned from past incidents that have shaped your current practices?
AK: We have implemented a Safety Management System that manages safety as an integral part of our overall business. Every irregularity in a case will undergo a comprehensive investigation and proper reporting to the authorities. Rather than seeking to assign blame, our priority lies in understanding the root cause and why it occurred. This approach allows us to formulate corrective and preventive actions based on lessons learned, which is crucial in preventing similar incidents from recurring.
Furthermore, we promote a culture of knowledge-sharing across our network. Best practice are shared network-wide because safety insights benefit everyone, and we maintain an internal database dedicated to continuous improvement.
PA: How does Cathay Cargo ensure transparent communication with clients regarding the intricate requirements and restrictions of shipping dangerous goods?
A.K.: At Cathay Cargo, safety remains our top priority. We continuously review the latest industry and regulatory requirements to ensure we uphold the most stringent safety standards. Our commitment extends beyond compliance – we believe that open communication and regular knowledge-sharing sessions with our customers on the latest safety requirements and best industry practices will further enhance the overall safety of the industry.
PA: In what ways does Cathay Cargo collaborate with international aviation and safety authorities to influence and shape policies concerning dangerous goods?
A.K.: We actively participate in the IATA DG Board meeting regularly, engaging with different stakeholders from CTO, airlines, and relevant authorities. These meetings serve as a platform for in-depth discussions on the DGR amendments and DG handling processes. Additionally, we participate in regular meetings conducted in Hong Kong with members of the CLG (Carrier Liaison Group)-DGWG (Dangerous Goods Working Group), where we exchange best practices and address safety-related issues to ensure the highest standards in DG transportation.
PA: What specific emergency scenarios has Cathay Cargo prepared for regarding dangerous goods, and how have these preparations influenced your broader operational strategies?
A.K.: The carriage of mis-declared and un-declared lithium batteries post significant safety threats to aviation safety. The agent needs to declare the battery models correctly so they can be identified and safely carried on our aircraft. We offer a complete suite of lithium battery carriage solutions to cater to the differing needs of our customers. This includes the fire containment bag (FCB), fire resistant container (FRC) and fire containment cover (FCC) to mitigate the fire risk. The FRC can take loads of up to 1,500kg and can passively contain a fire. It is also suitable, where permitted, for consolidation of loose or skid-size RBI cargo and general cargo in order to optimise flexibility and more efficient use of space.
PA: How does the handling of dangerous goods align with Cathay Cargo’s sustainability goals, especially regarding environmental impact reduction?
A.K.:Cathay’s commitment to sustainability leadership extends to our air cargo services, and is part of our commitment to tackling climate change by achieving net-zero carbon emissions by 2050. Fly Greener, our carbon-offset programme powered by an integrated carbon emissions calculator, was extended to air freight in 2022. Amongst other initiatives to reduce our environmental impact, our end-to-end digitisation project will help to significantly reduce paper waste.
Specific to dangerous goods, our handling process prioritises containment and spill prevention measures to protect the environment from potential releases or leaks.
P.A.: Are there any forthcoming changes or innovations within Cathay Cargo that aim to further enhance the safety and efficiency of dangerous goods transportation?
A.K.: The Dangerous Goods Digitisation Project has been launched with the goal of implementing the digitisation transformation of the Dangerous Goods end-to-end handling process. The initiative aims to establish a centralised platform for managing all data, digitised documents to improve data quality and traceability, and enhance operation efficiency.
This story was first published in the July-August 2024 issue of Payload Asia.