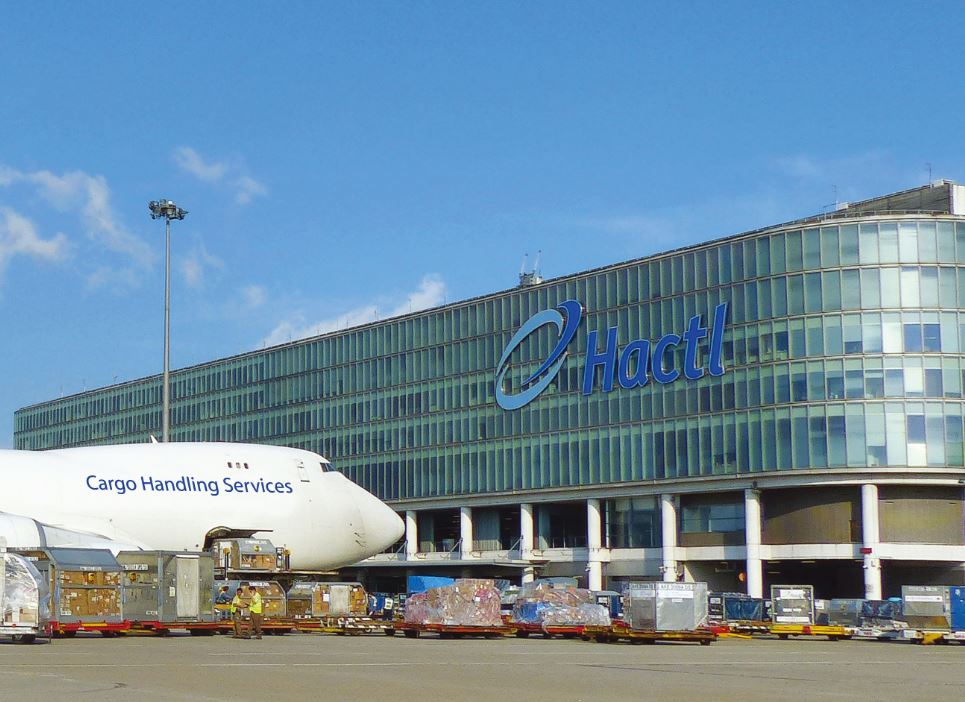
For six straight years, Hong Kong has led the air cargo world as a top cargo hub – producing enviable volumes that challenge most other airports to attain. Hong Kong’s location certainly provides major advantages – such as being central to the buoyant economies of Asia, and also the bilingual and well-served gateway to China. Th e presence of the Hong Kong Air Cargo Terminals Limited (Hactl) is also an added advantage – the company has a proud 40-year history of investment and innovation and is well regarded globally as the benchmark for all aspects of ground handling.
Seizing opportunities in the East
As the only ground handler in Hong Kong not wholly or substantially owned by an airline, Hactl prides itself on being able to provide neutrality to all 100 airlines they’re currently serving. Having started the year off on a positive note, Hactl is currently up 16% year-on-year; that is 700,000 tonnes as at end of May 2017, and are optimistic the upward trend will continue.
The handler has found several ways to capitalise on opportunities, including cementing a position as the gateway to the mainland. Th rough its logistics subsidiary, Hacis, Hactl has the advantage of being able to off er customers catchment into southern China. Speaking about Hacis, Mark Whitehead, CEO said, “Our valueadded logistics subsidiary Hacis plays a key role in moving mainland mail containing e-commerce electronics. Mainland Chinese airports often have no direct fl ights to service this business but Hacis has made Hong Kong a viable export point for this mail- 1000 bags of it every day.”
Rising volumes in China’s booming e-commerce sector demonstrate the increased demand for goods from the region to other markets. According to a report by eMarketer, Deloitte Research, China will remain the world’s largest retail e-commerce market. Sales topped USD$899.09 billion in 2016, representing almost half (47%) of digital retail sales worldwide.
Off the back of China’s increasing global e-commerce demands, the handler, combined with its logistics subsidiary have found a niche by providing a one-stop solution to carriers. Hacis provides integrated logistics support services to more than 200 airlines and freight forwarders – with cargo businesses benefi ting from the unique logistics solutions. Th e increase in both inbound and outbound traffi c has also boosted revenues and in turn, increased customers’ needs.
The Hacis SuperLink China Direct off ers an expedited road feeder service for air cargo routeing via Hong Kong to connect to the mainland. This provides a hassle-free solution for airlines and freight forwarders to handle and transport a wide range of freight types between global markets and China. Th rough the service, cargo is continually transported between the air cargo terminal in Hong Kong and Customs-bonded Inland Cargo Depots in China. Th is is made possible via the Intermodal Transshipment Facilitation Scheme in Hong Kong and Quick Pass mode in China.
Furthermore, the trucks are equipped with Customs GPS E-seal that increases cargo security and provides real-time shipment status during transportation. Th e GPS E-seal also increases speed by sending declaration and digital truck manifest in advance to related custom departments – crossing the borders in a seamless fashion.
Development plans in the Pearl River Delta (PRD) are underway and on completion, will result in the expansion of the road, rail, seaport and airport capacities in the region. Th e project consists of building the new Hong Kong- Zhuhai-Macau Bridge, linking Hong Kong, Macau and the PRD by 2020. An immediate benefi t for Hacis will be the reduced trucking times from two hours to 40 minutes.
Whitehead said, “The new bridge will certainly add to opportunities for Hacis, which operates express road feeder services (SuperLink China Direct) over the industrialised areas of southern China. By making the western PRD more accessible, it adds to the appeal of Hong Kong as the region’s hub. However, if Hong Kong suff ers a shortage of slots for freighters in the run-up to the opening of the third runway, Hacis can also operate as a capacity and demand balancing mechanism, quickly and cost-eff ectively moving cargo.”
Unending drive for improvement through innovation
Hactl believes that e-Freight is the way forward for the air cargo industry to fi nally enter the digital era – it is fast, accurate and effi cient. “Th e fact that the industry is stalled at around 40% implementation of eAWB, suggests there are industry-level obstacles which have not been resolved,” Whitehead elaborates. Despite the handler being fully eAWB ready and capable of joining a paperless supply chain, Hactl can only proceed if and when all the stakeholders are on equal footing.
With a technologically advanced terminal, which is the most productive in the world, Hactl must keep abreast of advances and invest in the right technology. Th is is possible through a dedicated Performance Enhancement (PE) department – whose sole purpose is to question every move Hactl makes and constantly implement improvements. Th is department is behind the adoption of mobile computing throughout the terminal and ramp operations, through the COSAC-Mobile application.
Th e implementation of the COSACMobile application enables staff and customers to check fl ight status, pre-book arrival for deliveries and collections, gain access to a fast lane into truck parking, as well as being directed straight to an available dock. Th is has revolutionised Hactls’ business processes, reducing costs and emissions, increasing productivity and greatly enhancing customer service.
Additionally, the mobile app has improved truck fl ow management in Hactl by speeding up vehicle processing, enhancing security and improving parking capacity during peak hours at SuperTerminal 1. Th e average entry time for users has been reduced by 70% to fi ve seconds via pre-registration on COSACMobile and the fast-track entry lane which is fi tted with automated number plate recognition (ANPR).
The overhaul of the truck flow management also saw the installation of two new self-service kiosks next to the Truck Control Office (TCO), enabling truckers to register their vehicle for shipment collections and quickly check statuses. An automated system calls parked registered trucks forward to a designated vacant loading bay via Smartphone notifi cations and voice announcements. Th e use of these self-service kiosks has reduced average vehicle processing time by two-thirds, compared to manned counters.
Another recent innovation Hactl has implemented is the automatic capture of photographic images of all cargo as it arrives and is check-weighed; allowing staff to recall the images on their mobile devices. Th is makes it easier to identify cargo, helps to avoid delays at pallet building stage by anticipating awkwardsized pieces, and provides useful evidence in the case of damage claims.
Training is another area which has benefi tted from Hactl’s innovation. To tackle the limited opportunity for new recruits to gain hands-on experience in activities such as ramp handling – which can be challenging in the fast-paced and potentially hazardous ramp environment – Hactl has partnered with a multimedia company to develop a Virtual Reality (VR) based training application for ramp handling.
This has enabled new staff to experience the live handling environment and practice simulated activities from the safety of a training suite. It provides greater fl exibility in scheduling training sessions and increased opportunities for practice without relying on aircraft availability.
Calvin Lok, Hactl’s Assistant Manager for Learning and Development explains that “VR Training improves our training fl exibility, raises the learning pace, and allows trainees to practice the handling of odd-sized cargo pallets, as well as enhancing their emergency ability and safety awareness.”
Overcoming industry challenges
Th e biggest challenge in the air cargo industry is the ability to anticipate fastchanging market conditions. Increasing regulations driven by security and safety issues as they arise, force industry players to comply with regulations that are becoming more stringent. Stakeholders in the logistics business are obligated to do their part in increasing effi ciency in the supply chain while complying with regulations. “Compliance and the adoption of best practice are in our genes and we embrace all new standards that can result in new business opportunities for our customers,” said Whitehead.
Hactl, throughout its 40-year history, has always chosen leadership and was the fi rst handler in Hong Kong to be both certifi ed under the IATA Ground Operations Manual (IGOM) and obtain the IATA CEIV Pharma Validation. Th e handler sees it as their duty to make their carriers as competitive as possible and set an example for the industry.
This can be seen in the point to point pharma supply chain; it serves no purpose for the fi rst handler to be better equipped or more qualifi ed than the handler at the opposite end of the route. Whitehead went on to say, “We all need to be the same. So, leading is not about gaining advantage so much as driving necessary change in the industry.”
Following the election of President Trump, USA withdrew from the Trans- Pacifi c Partnership negotiations. Stalling of the TPP has given rise to the Regional Comprehensive Economic Partnership (RCEP), which builds on existing trade deals between the 10 ASEAN countries and six of their neighbours. “Th e RCEP could possibly replace the lost trade opportunities with the USA, allowing China and its neighbours to ultimately fare better. From Hactl’s perspective, all trade is good, and trade fl ow switching lanes or reversing is not necessarily a showstopper,” reckons Whitehead.
A more local challenge is recruitment; in Hong Kong’s zero unemployment economy, airport jobs can be hard to fi ll, because they involve commuting, often unsociable hours, and sometimes outside work in bad weather. While other handlers have resorted to the quick-fi x of agency labour, Hactl works hard to attract and keep its workforce – some of whom are original employees from the company’s early days. “Staff retention is so important,” says Whitehead. “We train our people, we invest in them, we off er real progression – and they stay. Th at’s good for Hactl and its customers, because there’s continuity, and because our staff develop and build experience, which equates to better service.”
The air cargo industry undergoes constant change and new challengesthe opening of new markets, airports vie for traffi c, new technologies lure business to other modes, and evertighter regulation threatens the industry’s core competence of speed. Despite all that, Hactl remains optimistic that through its continuing quest for process optimisation, its collaboration with carriers on new product off erings, and obsessive focus on quality, it will share in Hong Kong’s long-term success and prosperity. “You evolve, or you die: ask any dinosaur. So Hactl is evolving,” said Whitehead.
On a side-note:
“Our industry is founded on its ability to cope with the unexpectedfrom a single urgent spare part for a broken-down oil rig, to replacing a global supply chain broken by the failure of an ocean carrier. But that makes forecasting and budgeting very hard. That aside, the industry needs to fi nd ways of repairing its ailing yields, so that these justify the kind of investment the industry and its customers need for reliability, sustainability and progress.” – Mark Whitehead – CEO Hactl.