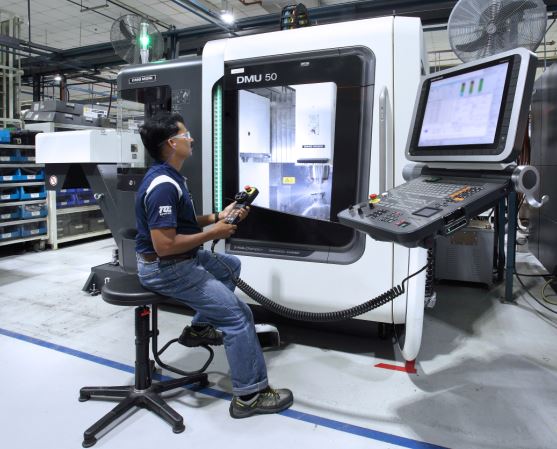
Pratt & Whitney Turbine Overhaul Services, a Singapore-based aircraft engine airfoil components repair specialist, has boosted its operations with an automated inspection system, laser cladding technology and improved Electron Beam Physical Vapor Deposition capabilities. Pratt & Whitney Turbine Overhaul Services is a joint venture between Pratt & Whitney and Singapore Technologies Aerospace.
“Pratt & Whitney has been at the forefront of the industry. We continue to innovate to not only meet, but exceed, customer demands of speed and reliability. A higher degree of automation bolsters our efficiency and ability to provide high quality and consistently repeatable results,” said Brendon McWilliam, senior director, Aftermarket Operations Asia-Pacific, Pratt & Whitney. “Our advanced Electron Beam Physical Vapor Deposition capability will allow us to apply coatings for existing engines, including the Geared Turbofan™ engines.”
Manual operations have given way to automated processes at this facility. Prior to using an automated inspection system, inspectors had to painstakingly measure the internal wall thicknesses of specific components using a hand-held probe. With the automated inspection system, inspectors simply place the parts to be measured into the machine which automatically carries out a wall thickness inspection on the required areas. The system has since reduced inspection process time cycle by 10 percent. The automated inspection system requires fewer tools, and as a result, is also helping to save costs arising from the maintenance and calibration of those tools.
Traditional welding operations have been replaced with laser cladding technology. Technicians used to manually weld materials together, a process which is highly dependent on the individual’s skill. With the laser cladding machine, staff can now perform the task with minimal supervision to achieve lower re-work rates. Similar to additive manufacturing, this laser technology deposits coatings on blade tips at a close-to-99 percent first-time pass rate. The overall downstream process cycle, and product cycle time has also been reduced.
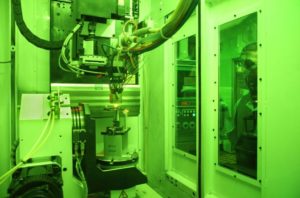
The improved Electron Beam Physical Vapor Deposition offering will enable the application of thermal barrier ceramic coatings on engine components to protect surfaces against corrosive environments for current and new Geared Turbofan™ engines. The process increases the length of time between repairs for these components and helps to increase overall durability.