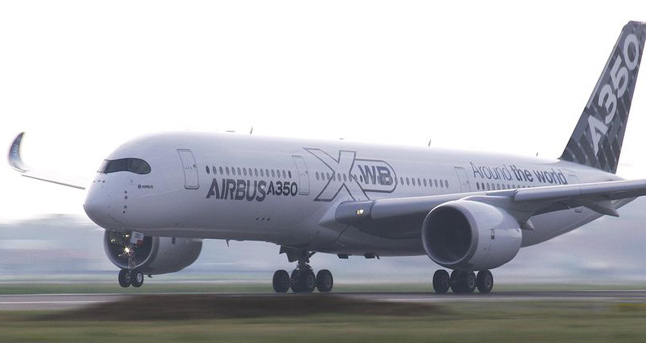
The wings for Airbus’ first A350-1000 have begun the process of assembly at Broughton, UK. The A350-1000 wing has the same span of the A350-900 that is already in service, but 90 per cent of the parts have been modified and the trailing edge has been extended to resize the wing for the additional payload and range.
At 32 metres long by six metres wide, the A350 XWB wing is the largest single part made from carbon fibre composite material in use in civil aviation today. They are designed and developed at Airbus’ facility in Filton, near Bristol, where a number of other systems are designed and tested including fuel systems and landing gear.
The high-performance wings of the A350 XWB make the aircraft faster, more efficient and quieter, according to Airbus. The wing design includes several streamlined features, among these are droop-nose leading edge devices and new adaptive dropped-hinge flaps, which increase the jetliner’s efficiency at low speeds.
To improve efficiency at higher speeds, the A350 XWB can deflect its wing flaps differentially, optimising the wing profile and providing better load control.